Application of TETRANCA frequency inverter in air compressor
Air compressors are commonly used in many industries such as machinery manufacturing, automatic production line, glass, ceramics, clothing, toys, plastics and so on. The factories generally have 10-30% margin for air compressors when designing, in addition, there are seasonal and temporal fluctuations in the actual demand of the factories, which also leads to large fluctuations in the amount of gas used, so most of the time the air compressor is not running at full capacity, and there is a lot of space for energy saving.
Traditional air compressors also have a lot of problems, mainly as follows:
- Frequency start-up impact current is large; although the main motor adopts Y-△ reduced voltage starting or reduced voltage starting, but the starting current is still very large, the impact on the power grid is large, easy to cause instability of the power grid as well as a threat to the operation of other power equipment safety. For self-generation plants, several times the rated current impact may also cause other equipment abnormalities;
- Consumption of electrical energy during loading and unloading; after the pressure reaches the required working pressure, the traditional control method determines that its pressure will continue to rise until the unloading pressure. During the pressurization process, more heat and noise are bound to be generated, which leads to loss of electrical energy. On the other hand, the pressure of a high pressure gas needs to be depressurized by a pressure reducing valve before it enters the pneumatic element, a process that also consumes energy. When the unloading pressure is reached, the air compressor automatically opens the unloading valve, leaving the motor idling, resulting in a serious waste of energy. The power consumption of the unloading of the air compressor accounts for about 30% to 50% of the full load, so it can be seen that the traditional air compressor has obvious energy saving space.
- unstable pressure, the bottom of the degree of automation; traditional air compressor automation is low, the output pressure adjustment is realized by the control of the loading and unloading valves, control valves, the adjustment speed is slow, fluctuations, low precision, the output pressure is not stable.
- Large amount of equipment maintenance; air compressor frequency starting current is large, up to 5-8 times the rated current, the way of work determines the loading and unloading valves are bound to act repeatedly, the parts are easy to deteriorate, the frequency and high speed operation, the bearing wear and tear, large amount of equipment maintenance.
The working process is to use the pressure sensor device to detect the pressure of the pipeline network, by detecting and displaying the analog signal of the reaction output pressure will be transmitted to the frequency converter, the frequency converter according to the feedback signal and the set signal to compare the use of the frequency converter internal PID for automatic output frequency adjustment in order to realize the automatic adjustment of the speed of the compression motor and the output power, to form a closed-loop feedback system to maintain the pressure of the network and the automatic control of the pressure. Automatic control.
The use of frequency converter transformation has the following advantages:
- small starting current, no impact on the power grid; frequency converter starting motor current rises gently, the impact on the power grid is small;
- stable output pressure; the use of frequency control system, you can real-time monitoring of the pressure of the gas in the gas supply pipeline, so that the pressure of the gas in the gas supply pipeline to maintain a constant, improve production efficiency and product quality;
- small maintenance of the equipment; the frequency converter soft start of the compressor, the pressure of the equipment to maintain a constant pressure and automatic control. Soft start of the air compressor, small impact on the equipment. Because of automatic frequency reduction, loading and unloading valves do not need repeated action, bearing wear and tear is small, the service life of the equipment is extended, and the maintenance workload becomes small;
- energy saving; the air compressor basically belongs to the constant torque load, the frequency conversion speed control method according to the size of the gas supply to regulate the motor speed, which can make the motor’s output power is basically directly proportional to the rotational speed (the amount of gas supply). When the volume of air consumption decreases, the exhaust port pressure rises, through the closed-loop feedback to the inverter, so that the motor speed decreases, reducing the output power of the shaft; when the volume of air consumption increases, the exhaust port pressure decreases, through the closed-loop feedback to the inverter, so that the motor speed increases, increasing the output power of the shaft. Therefore, the inverter air compressor system through the pressure closed-loop, real-time tracking of the air supply system load changes, adjust the speed of the air compressor motor to ensure that the exhaust port pressure is constant, so that the compressor motor works in the most economical operating conditions. It avoids frequent loading and unloading, frequent starting and stopping of the air compressor in the original control mode, which makes the power absorbed from the power grid drop greatly.
- Provide powerful and sensitive software/hardware protection functions such as current limiting protection, over-current and over-voltage protection, short-circuit protection to ground, overload protection, short-circuit protection of IGBT, abnormal current detection, abnormal relay suction, etc., to ensure the stability and reliability of the compressor system.
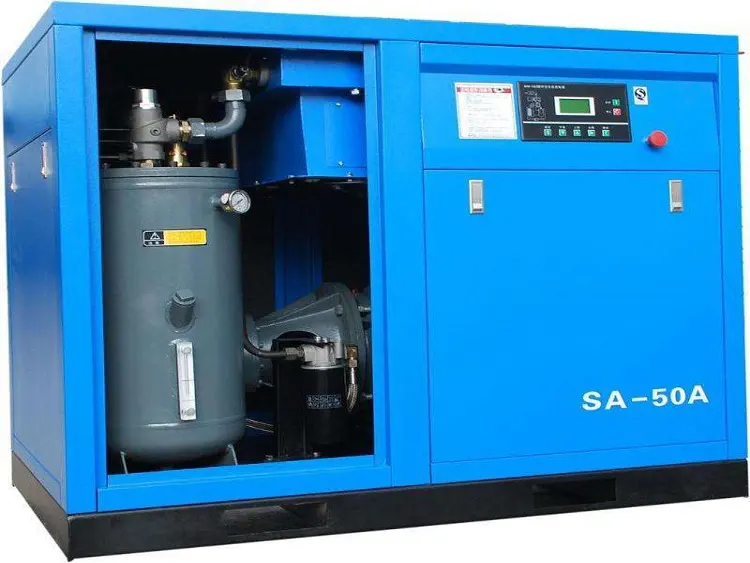